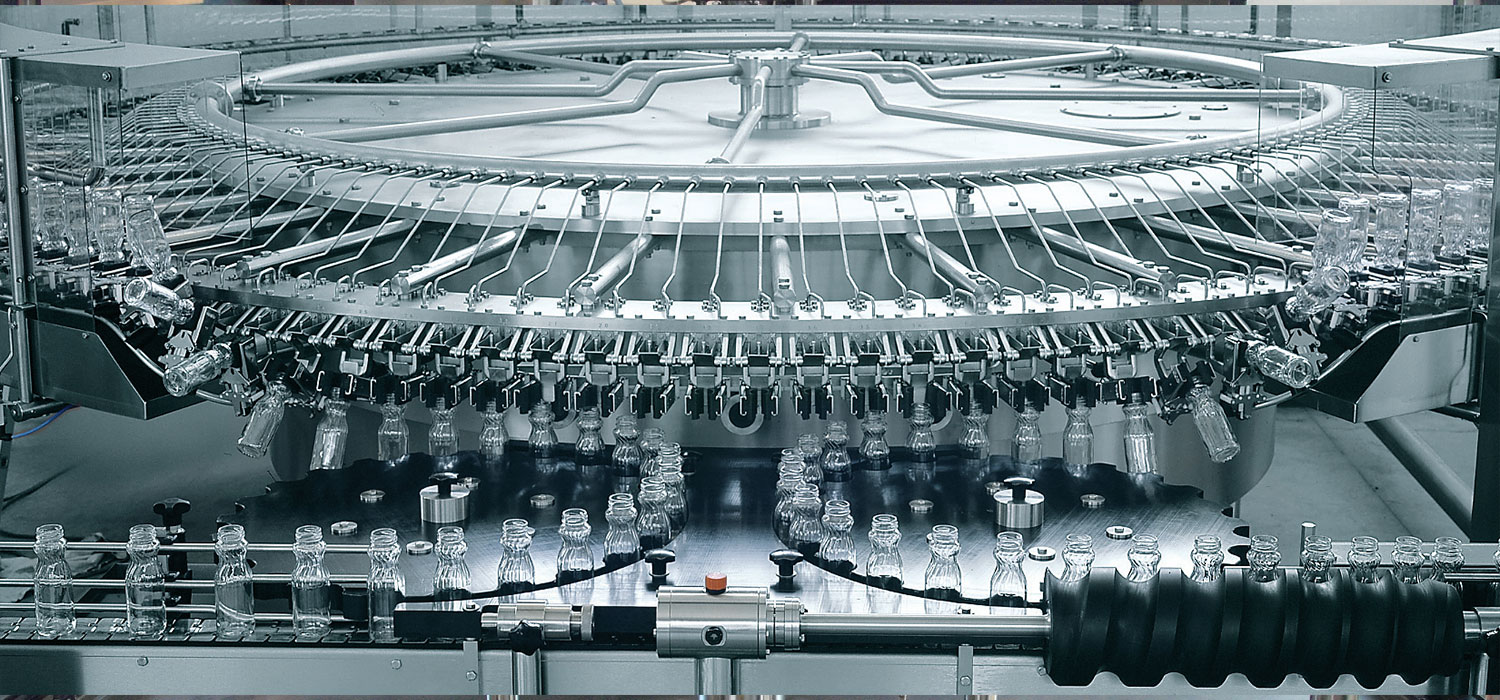
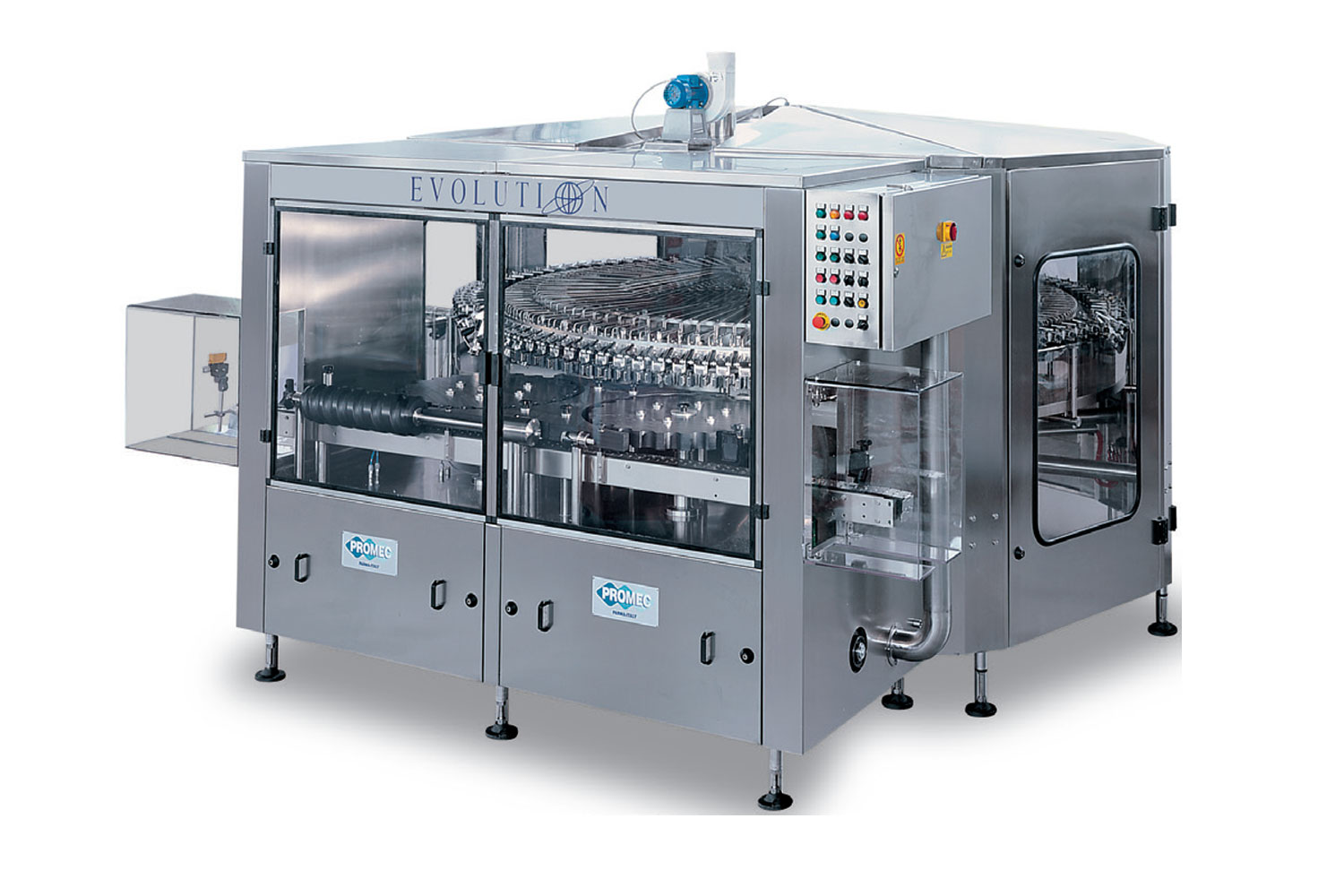
Evolution is a rotary rinser-blower-sterilizer characterized by grippers with a symmetrical and irreversible opening action, which grasp the bottles by the neck and rotate them on their own axis, both in fixed and mobile nozzle versions, so as to reduce and optimize the space required by the machine. The symmetrical opening of the grippers allows to process bottles with big sized necks; the irreversibility allows, instead, to process heavy bottles.
Thanks to the mobile nozzle, spraying can begin when the bottle is horizontal, thereby increasing treatment times.
Advantages of the Evolution rinser:
- Irreversibility of the movement. Bottles of any size and weight can be handled extremely safely.
- Rotary movement of the grippers on the bottle axis. On both the fixed and mobile nozzle versions, the grippers rotate around the bottle axis, so that the bottle always remains on the same axis even in the working position, thereby allowing the machine pitch to be used to maximum advantage.
- Longer treatment times. The new position of the rotating forks makes it possible to reduce the rotation angle of the container, thereby increasing the working angle without having to increase the size of the machine.
- Variable treatment times Partial treatment times can be changed very easily by adjusting the closing cam of the spraying valves, varying the angle of their position.
- Both fixed and mobile nozzle versions with an extremely small pitch are available.
- Minimum effort and power absorption. Since the bottle gripping force is provided by the mechanical irreversibility of the gripper, the closing spring (which is also the only one used) does not require much effort, so it does not absorb any power, thereby guaranteeing energy savings.
Every detail has been designed to ensure a high degree of hygiene, which makes this machine particularly suitable for applications in “aseptic environments”.
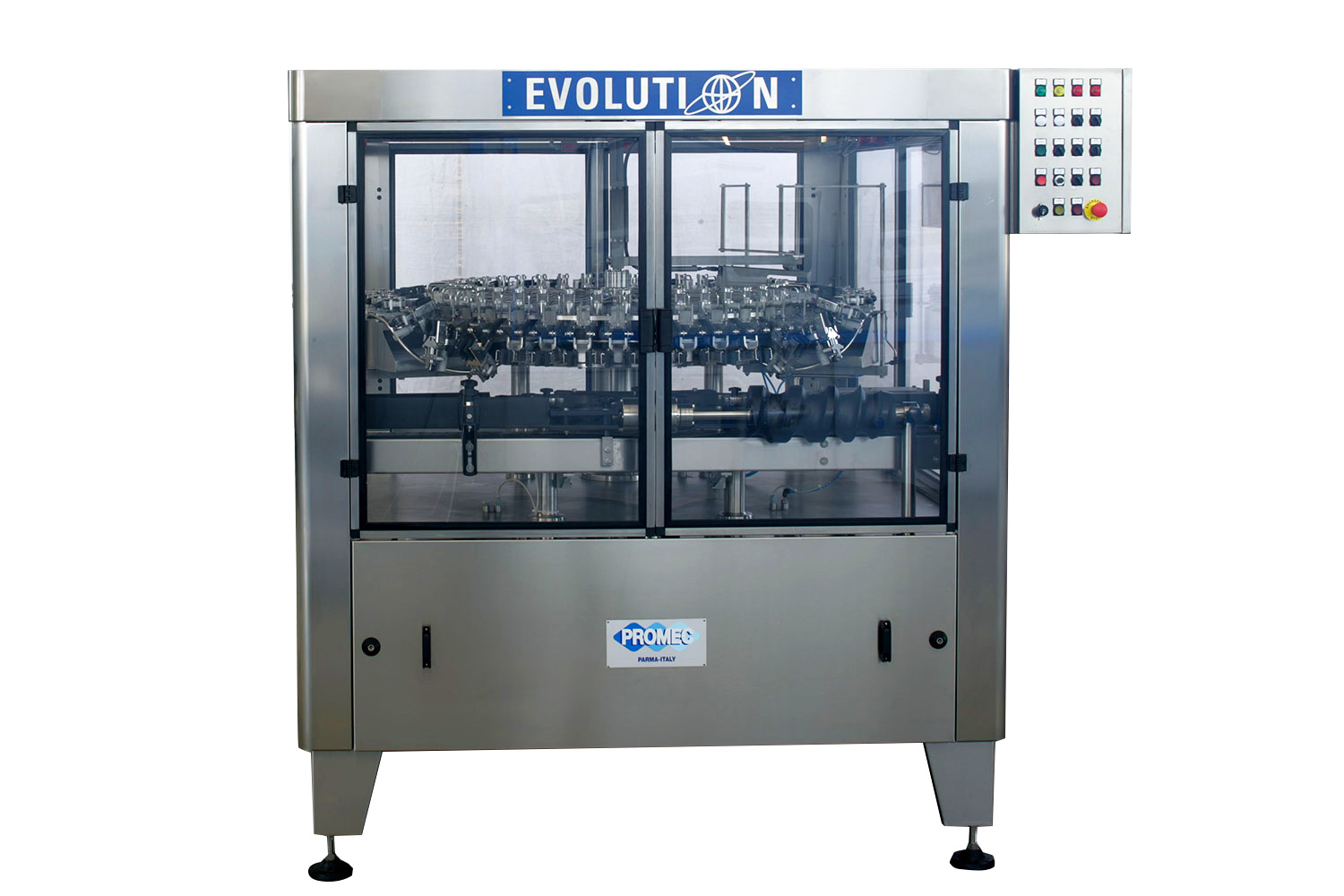
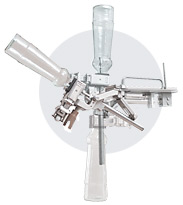
Mobile nozzle Evolution gripper with synchronized rotation of the nozzle
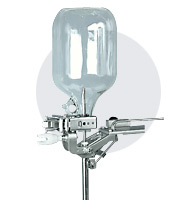
Mobile nozzle Evolution gripper with synchronized rotation of the nozzle
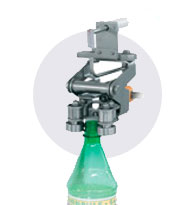
Evolution P.E. the ideal solution for PET bottles.
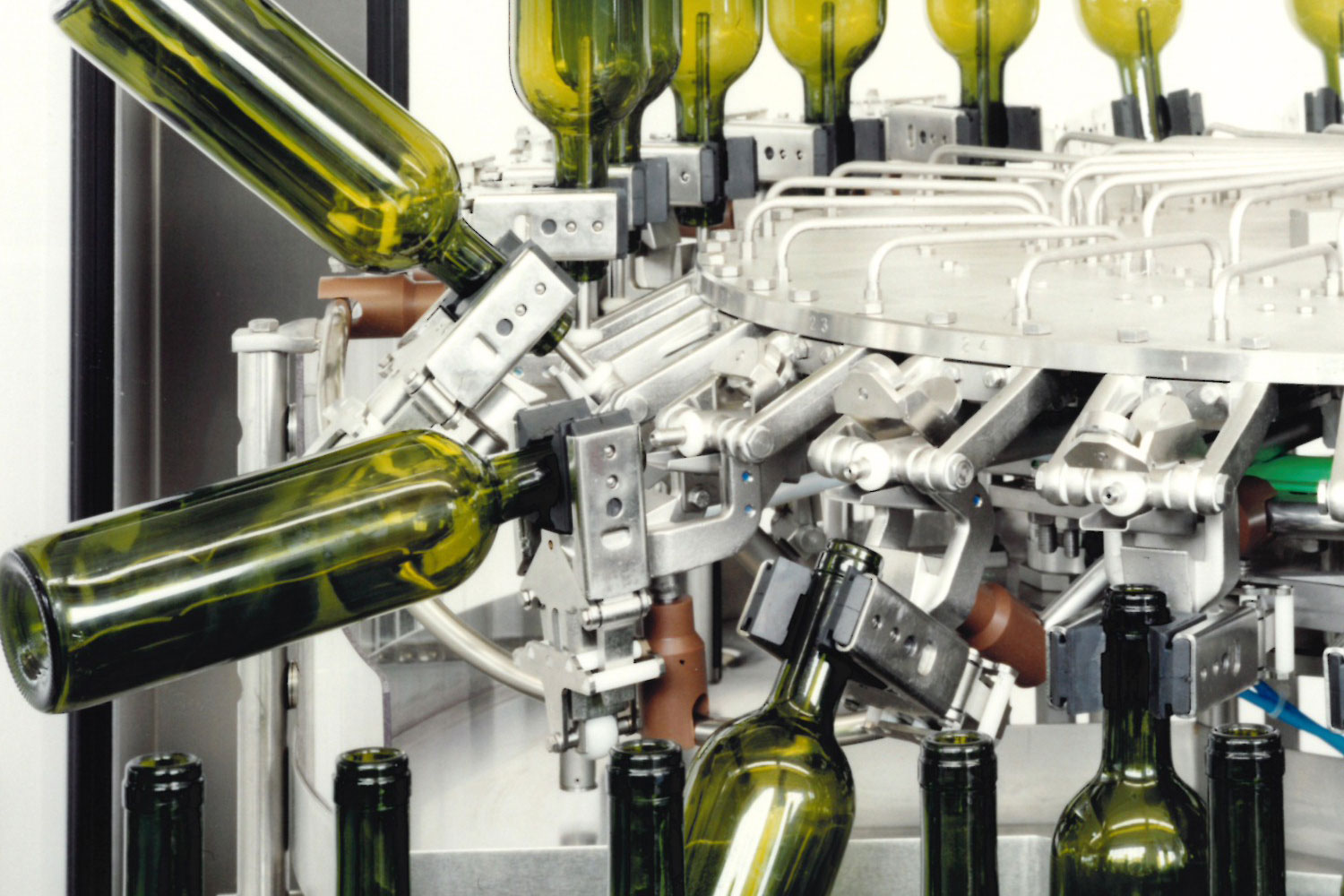
Mobile nozzle for glass
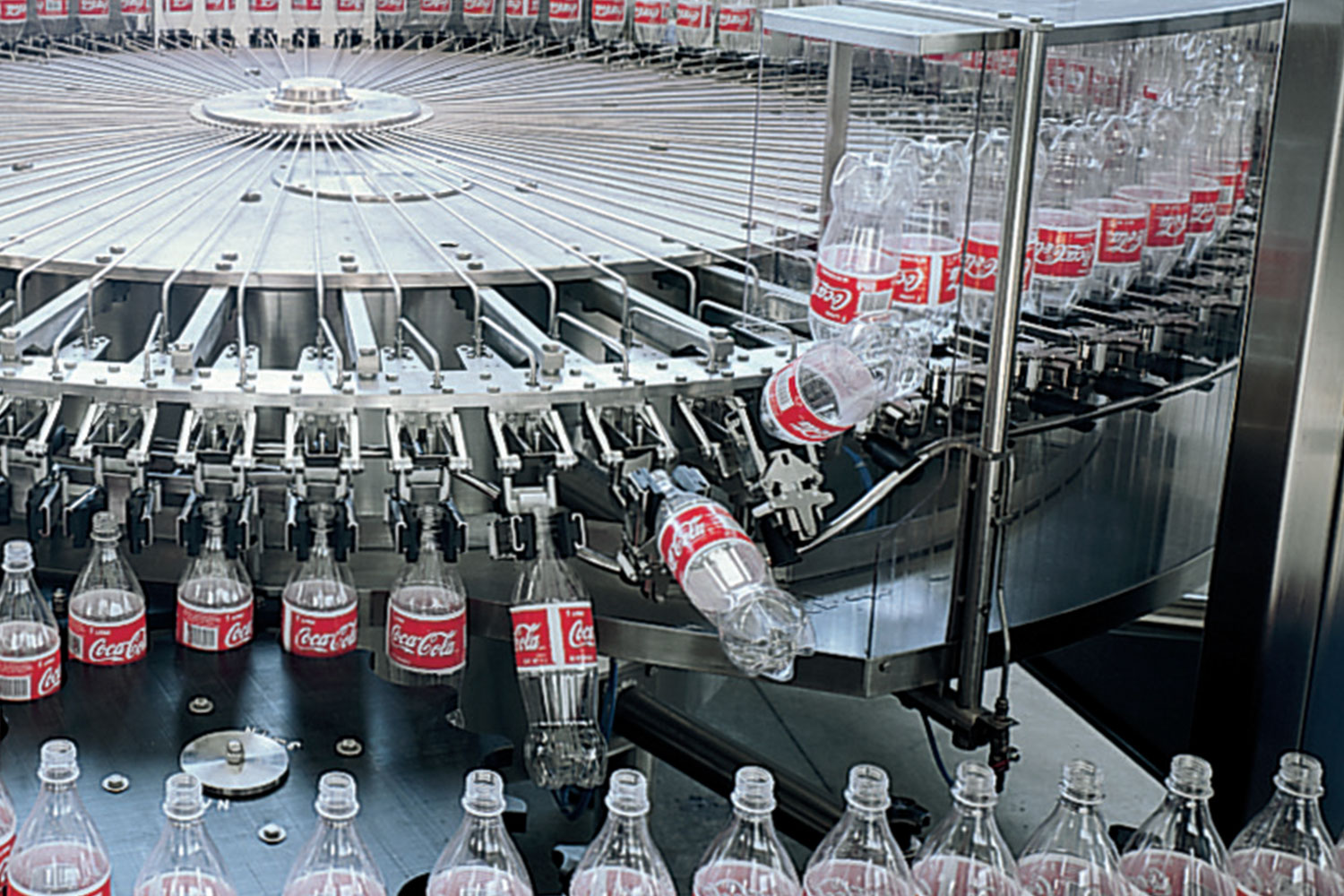
Fixed nozzle for PET
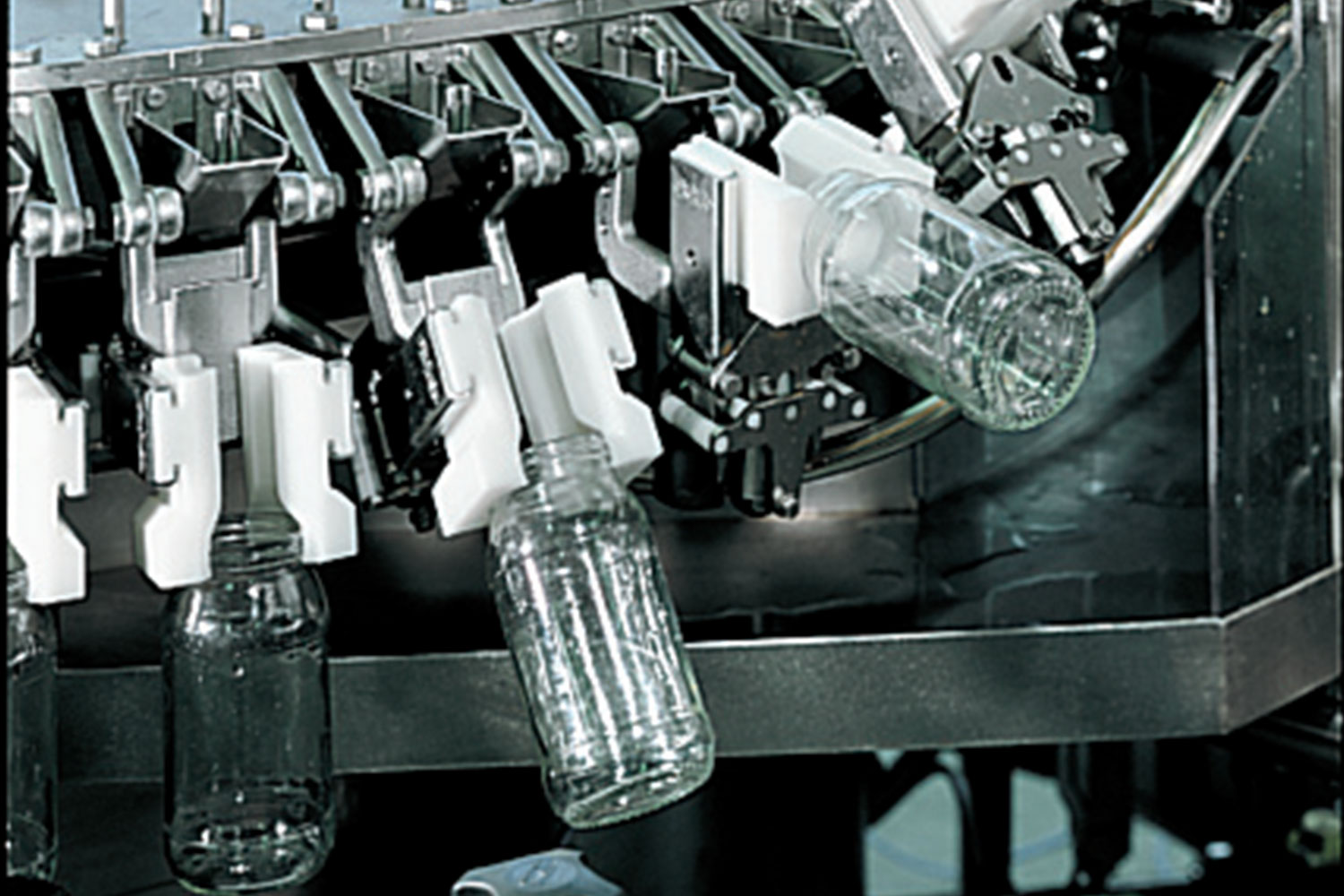
Fixed nozzle version
Evolution P.E
Designed and manufactured for the treatment of PET bottles, patented EVOLUTION P.E. grippers are characterized by holding the bottles exclusively by the neck and by the absence of any mobile part or any size change over. The neck gripping is granted by two stainless steel rollers that develop the clamping by means of pliable components upon which the rollers are installed.
The bottle is pushed inside the two rollers at the entry star with a slight pressure and is taken out in the same way by the exit star. Due to their design and AISI 316 standard construction these grippers allow for reduced maintenance costs and greatly improve machine sanitation. They also minimize machine from stoppages due to deformed or misplaced bottles.
Evolution P.E. ” the ideal solution for PET bottles.
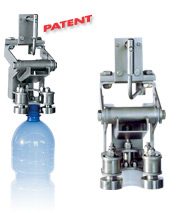
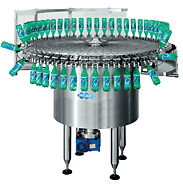
FLOW EFFICIENCY CONTROL SYSTEM
Through the flow control device (patented), linked to each spraying valve, it is possible to ensure that the nozzles are working properly and to check the efficacy of the cleansing fluid injection in each container treated, in order to guarantee thorough cleaning of the same.
A spherical mobile element is installed on the feed pipe of each nozzle and it is activated “only and exclusively” when the washing fluid flows out of the respective nozzle; a special sensor, positioned in the rinsing (or blowing) area, verifies the correct position of the mobile element, and hence the optimal operation of the nozzle.
If, on the other hand, the mobile element is not in the correct position, the malfunctioning of the corresponding nozzle is reported by means of an electric signal; this signal can operate an automatic ejection device of the bottle which has not been properly treated or it can stop the machine in a preset position so as to enable the operator to remove the unwashed container.
This simple and efficacious system is particularly suited for applications in which it is of fundamental importance to guarantee that the containers have been treated (e.g. in the ULTRACLEAN and ASEPTIC sectors), so as to avoid problems relating to the contamination of the bottled product and the duration of its shelf life.
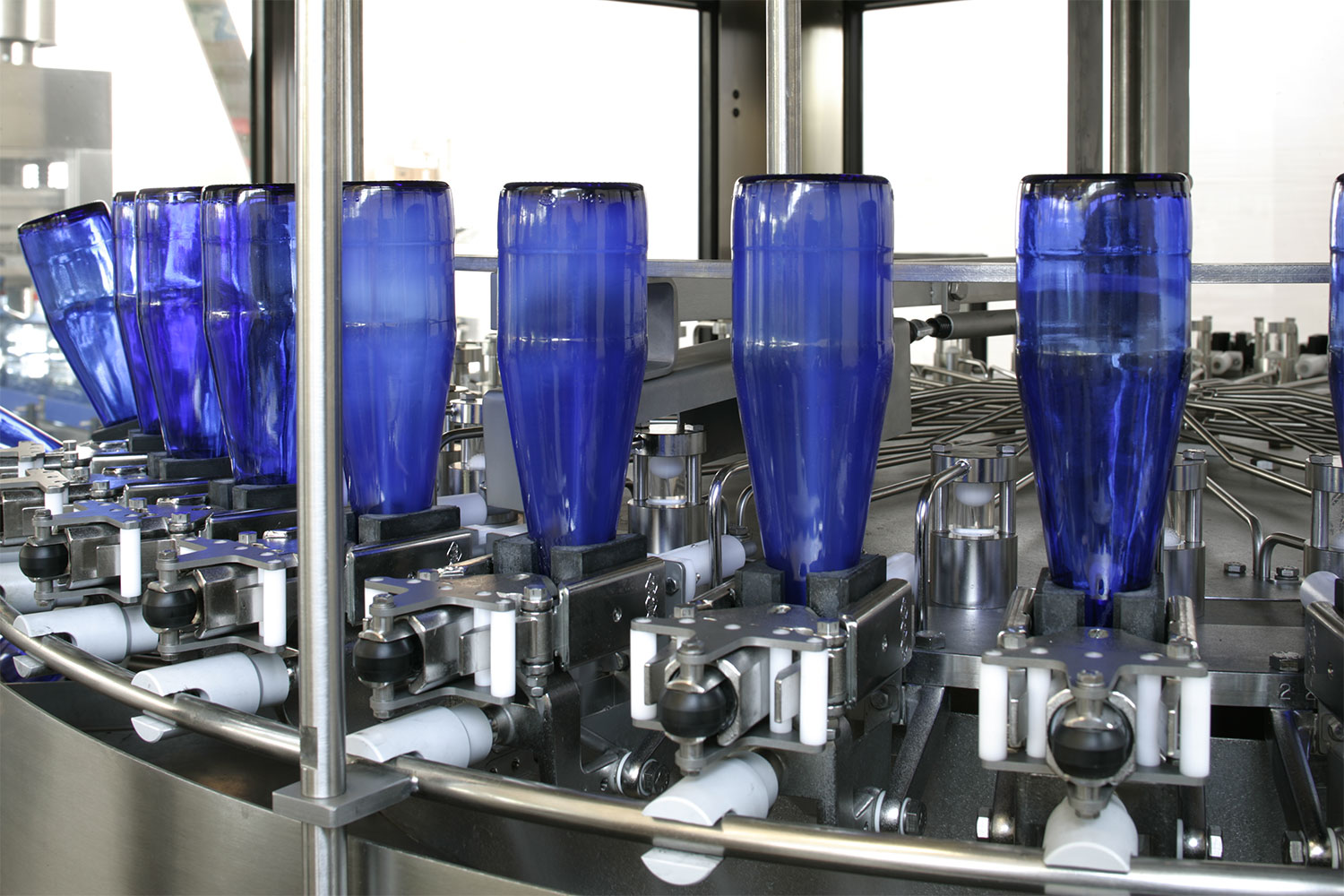
Flow efficiency control system detail
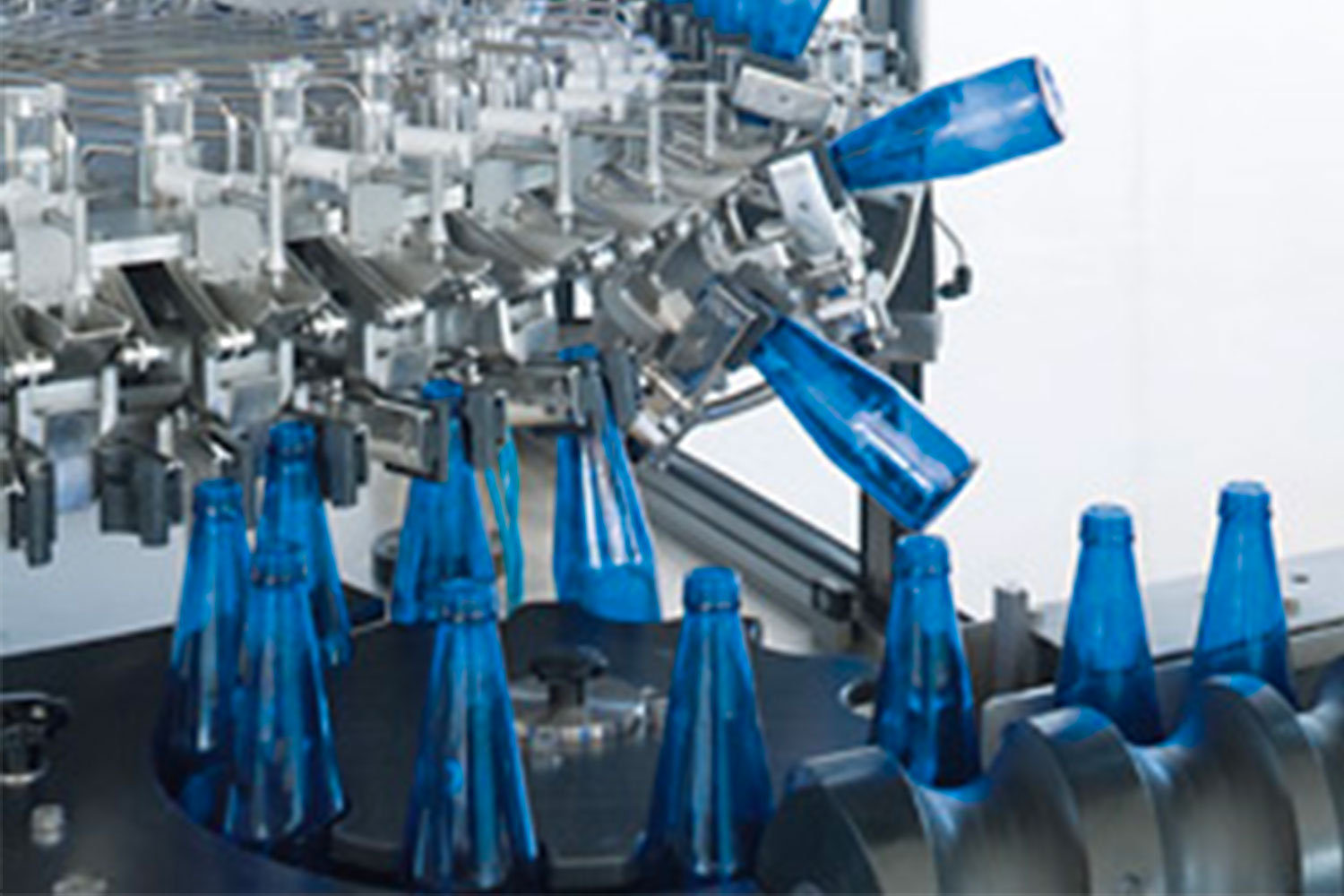
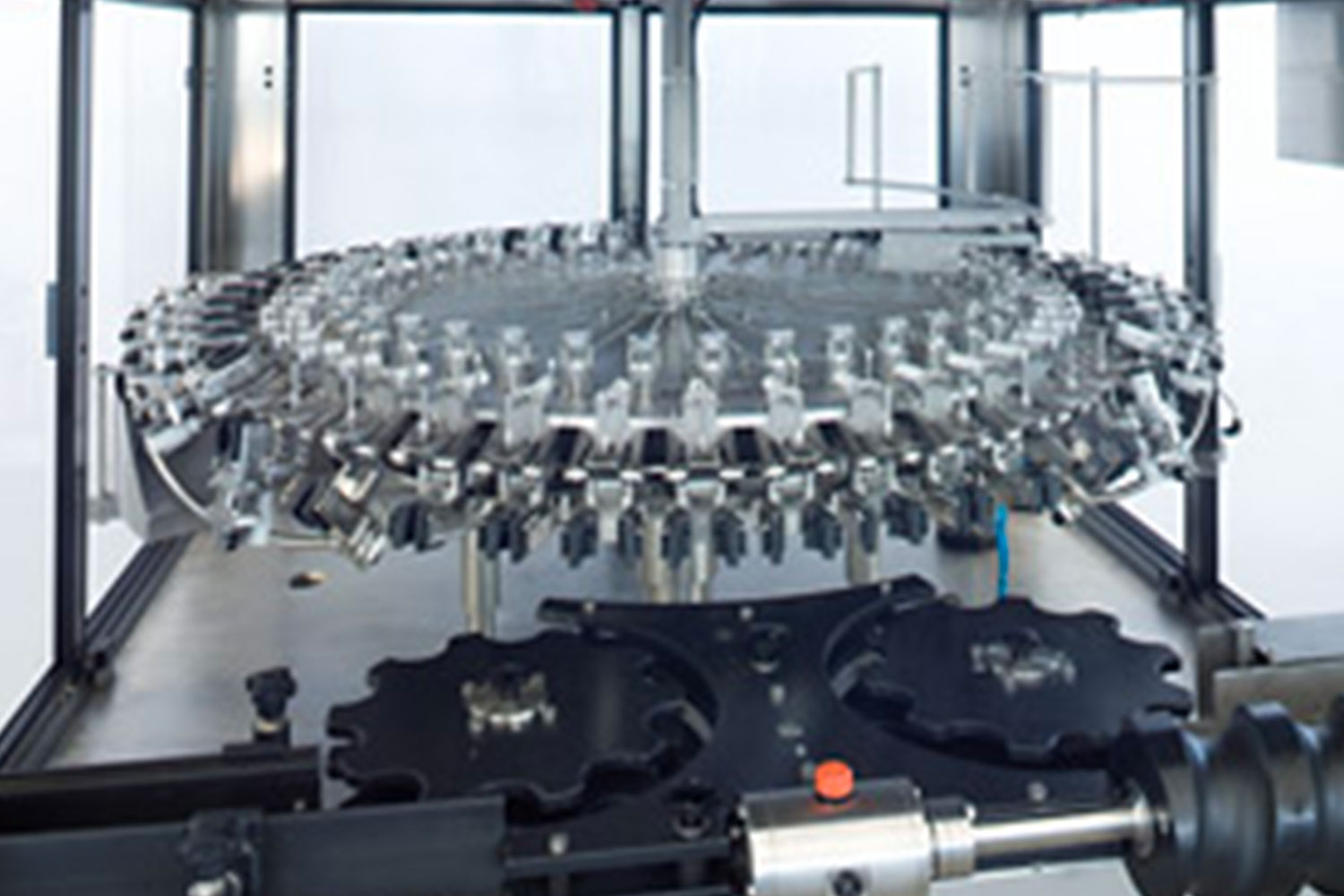
Fill in the form to receive all the details you need about all Promec bottling machinery
FILL IN THE FORM1R – Fixed and mobile nozzle
One rinsing phase with fresh water (to drain) or with sterilizing solution (water+ozone, water+sulphur dioxide, chlorinated water) followed by a drainage time dependant upon the acceptable residual water content.
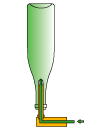
1S (1S+1A) Mobile nozzle
One blowing phase with sterile air, sterilizing gas or steam to remove any dust or harmful gas from bottles and it is the case, make them sterilized. In order to remove the injected gas and any particles in suspension, it is possible that blowing and suction phases take place alternately. (1S+1A).
1R + 1S (1V) Mobile nozzle
One rinsing phase with fresh water (to drain) or with sterilizing solution followed by a blowing phase with sterile air to make easy the drainage, or with sterilizing gas (1R+1S) or steam to complete the container cleaning (1R+1V).
2R Fixed and mobile nozzle (2 ways)
One rinsing phase with sterilizing solution, either fresh or re-circulated, followed by a second rinsing phase with fresh water (to drain) and by a final drainage phase.
2S (1S+1V) Mobile nozzle (2 ways)
One blowing phase with sterile air to remove any residual or harmful gas from bottles followed by a second blowing phase with sterilizing gas (2S) or steam in order to make container sterilized (1S+1V).
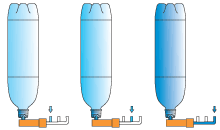
3R Fixed nozzle (3 ways)
Rinsing stage with a high-concentration of sterilization.
Solution followed by a second procedure of low concentration solution, and the final rinsing stage with sterile disposable water and a final dripping stage.
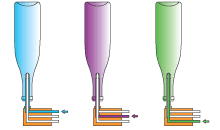
1R+1V+1S (1R) Mobile nozzle (3 ways)
A rinsing stage with hydrogen dioxide sterilising solution (H2O2), followed by a steam activation stage and a third sterile-air blowing (1S) or sterile water rinsing (1R) stage.